SECO/VACUUM News
HEXONIC Ltd. orders a vacuum furnace with fast delivery for dynamic product development
HEXONIC Ltd., a European manufacturer of heat exchangers who has been providing advanced and reliable heat exchanger technologies for various industries for 35 years, purchased a Vector vacuum furnace from SECO/WARWICK. The solution will be used mainly for brazing heat exchangers.
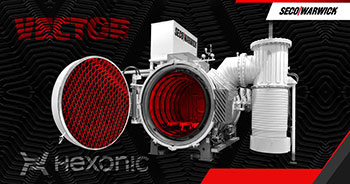
The furnace or order was covered by the fast delivery program, so the implementation was lightning fast. The furnace has been adapted to Hexonic’s specific expectations regarding high vacuum, and process cleanliness during soldering.
Tailor-made furnaces at your fingertips
Metal heat treatment furnaces are complex solutions which have many options for modifications. Often, the Partner’s specific needs require a special solution design meeting these expectations.
“SECO/WARWICK is one of a few manufacturers who have developed a strategy that allows furnaces to be quickly modified in order to meet specific needs based on a standard product portfolio. This means faster order execution and, consequently, increased profits resulting from its implementation at the Partner’s machinery park,” said Sławomir Woźniak, President of the SECO/WARWICK Group.
“This is our fourth delivery to Hexonic. It is unique because we used a furnace from the quick delivery program, which was built with express implementation in mind. We have adapted it to Hexonic needs and guidelines so that it meets all key criteria. We can apply a similar procedure to any standard product. For our customers this means a significant reduction in delivery time and greater furnace availability,” said Maciej Korecki, Vice-President of the SECO/WARWICK Vacuum Segment.
Vector – a vacuum furnace with many possibilities
The furnace purchased by Hexonic is based on a standard solution with a working space of 900x800x1500 mm, graphite insulation, graphite heating elements and specialized nozzles equipped with radiators, reducing the solder deposition. This fits perfectly into the customer’s specific needs regarding soldering processes. The round heating chamber allows the user to load oversized elements.
The characteristic features of this structure includes a high vacuum system that can achieve a high working vacuum of 10-5 mbar, convection heating up to 750 °C (a system which improves the heat transfer efficiency when heating at lower temperatures), and a dew point sensor (a system which solves one of heat treatment’s very critical requirements by preventing water vapor condensation which in turn, causes load surface oxidation.)
The use of an efficient cooling system with a pressure of 6 bar allows the system to significantly shorten the load cooling time, and thus significantly increase the furnace productivity.
“The Vector furnace will streamline and increase the soldering processing capacity, and improve the process economics, through energy savings and the graphite chamber efficiency, as well as the process cleanliness and velocity. It is a furnace based on our proven solution, with specially redesigned nozzles and power feedthroughs enabling an effective soldering process and ensuring reliable furnace operation in industrial conditions. We are a major manufacturer of equipment for metal heat treatment, so we can afford to build both standard equipment and special orders. We have many solutions in an advanced production cycle which we can quickly deliver to the customer. Importantly, we can modify each of them to meet specific production expectations,” commented Jędrzej Malinowski, Sales Manager of the SECO/WARWICK Vacuum Furnace Team.
Heat exchanger brazing from SECO/WARWICK
Aluminum heat exchanger brazing can be performed either in a protective atmosphere (CAB technology) or in vacuum (VAB technology). In the case of stainless exchangers, vacuum technologies are used. SECO/WARWICK has extensive experience supplying these technologies to heat exchanger manufacturers from many industries.
“We have been supplying specialized heat exchangers for various industries for over 35 years. We work for customers almost all over the world. Heat exchangers require high-quality joints, which we can achieve using brazing technology. We are cooperating with SECO/WARWICK for the fourth time, which in itself should be an excellent recommendation. This time we took advantage of the option to purchase a solution which was at an advanced production stage at the time of placing the order. Thanks to this, we received an offer with very fast delivery. Due to dynamic development and many orders, time played an important role for us. It is also important that despite the short delivery time, the furnace was adapted to our specific needs,” said Wojciech Zygmunt, Hexonic Operations Director.