SECO/VACUUM offers two configurations of vacuum oil quench furnaces. The two-chamber furnace, called D type, is a dual-chamber furnace with one chamber for vacuum heat processing and a second chamber for oil quenching or gas quenching. The three-chamber furnace, called T type, provides the same chambers as the D type plus a third pre-heating (and/or pre-oxidation chamber) which increases productivity through semi-continuous batch processing. In the three-chamber approach SECO/VACUUM’s PreNitLPC® process can be added for even higher productivity (see PreNitLPC®). The high-efficiency oil quench has an agitation system that ensures excellent oil recirculation throughout the workload which results in uniform and fast cooling.
Industries
- Aviation / Aerospace
- Automotive
- Energy
- Industrial Machines
- Gears
- Bearings
- Commercial Heat Treating
Applicable Technologies
- Vacuum Hardening with selectable oil quench or gas quench (also, see our high pressure gas quench page Vector LPC)
- Low pressure carburizing using FineCarb® with oil or gas quench (see FineCarb®)
- High-temperature carburizing up to 1050°C using PreNitLPC® with select case hardening steels with oil or even high pressure gas quench (see also Vector LPC)
- Carbonitriding with oil quench
- Bright hardening
- Oxidation in the preheating chamber
- Annealing
- Tempering
Advantages
- High volume throughput with semi-continuous operation
- High quality parts
- High-temperature carburizing for typical or special steels
- Economical processing
- Very low consumption of processing gas
- Furnace can be used up to 1320ºC (2,400ºF)
- Reduction of and repeatability of distortion
- Process simulators & fully automated processing (see FineCarb®)
- Flexibility, no furnace idling periods, quick start up & shut down of the furnace
- Meets AMS 2750E, AMS 2759, BAC 5621
- Quick workload-transport time from furnace to quench
- Lower distortion and no IGO (Intergranular Oxidation)Heat treatment produces uniform, high quality parts
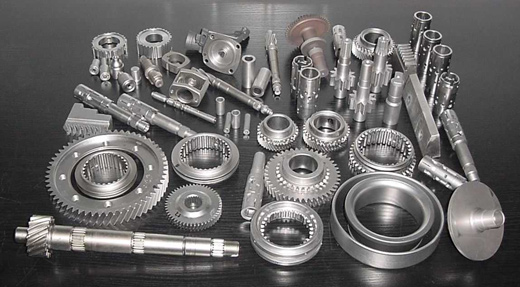
Typical parts processed in CaseMaster Evolution® furnaces
The CaseMaster Evolution is offered in many variations depending upon the end user needs and annual volumes desired.
Features:
The CaseMaster Evolution comes with vacuum processing and separate heating and quenching chambers (both oil quench and/or separate high pressure gas quench). (SECO/VACUUM also offers LPC case hardening technology in our Vector vacuum furnace line of single chamber high pressure gas quench furnaces). Shown below is the D-style for Double Chamber and the T-style for Triple Chamber, both shown with the standard vacuum oil quench.
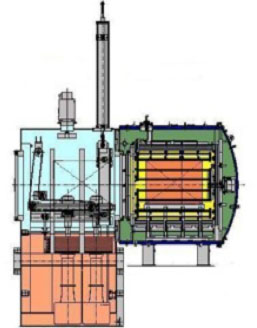 D-Type Double chamber for batch work processing with conventional loading over the Oil quench
|
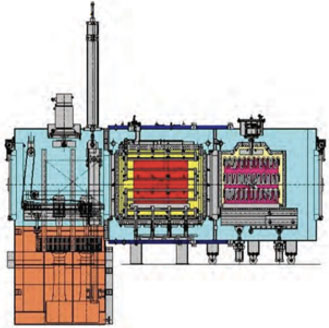 T-Type Triple chamber for continuous batch work. Oil quench or gas cooling/quenching with a separate chamber for:
- Loading and Pre-heating, pre-oxidation
- Pre-heating with PreNitLPC® technology
|
Furnace Options:
- Oil quenching
- Hot oil quenching
- High pressure gas only quench (separate gas quench chamber instead of oil)
- Dual (oil quench with 2 bar gas cool over the oil)
- Carburizing with FineCarb®
- Simulation/Recipes with SimCarb
- H2 partial pressure
- Special with oil and gas quench with high pressure third chamber gas quench (see photo)
- PreNitLPC®
Auxiliary Equipment:
- Tempering furnaces (air or vacuum)
- Parts Washers
- Closed loop water cooling systems
- Loading and unloading options
- Loading trays
- High pressure gas buffer tanks
- Fully Automated loading/multicell
- Cryotemper
- SECOVISORY consultation services
As a recap - CMe Furnace Benefits & Advantages:
- No Endothermic Generators needed!
- Low use of process gases (carbon media)
- High temperatures with no damage to furnace
- Nominal temperature up to 2400ºF (1320ºC)
- Reduction of distortion
- Process simulators & fully automated processing (see Carburizing tab)
- Flexibility, no idling needed on weekends, etc. Turn it on, turn it off
- Meets AMS 2750E, AMS 2759, BAC 5621
- Fast transport times to quench (less than 30 seconds)
- Compact, modular design
- Highly agitated oil circulation design
- 2 Bar cooling offers “Top Cooling”
Product Matrix
Style1
(D/T)
| 4
| 6
| 9
| 12
|
|
Width x Height x Length – inches (mm)
|
Workload Size2
|
12 x 12 x 18
(300 x 300 x 460)
|
16 x 16 x 24
(400 x 400 x 600)
|
24 x 24 x 36
(600 x 600 x 900)
|
36 x 36 x 48
(600 x 600 x 1200)
|
Maximum Gross Load – lbs. (kg)
|
200
(90)
|
450
(200)
|
1350
(600)
|
2650
(1200)
|
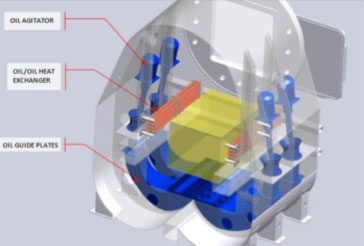 Oil Quench Explained |
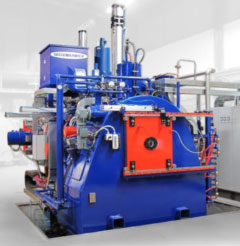 CMe with separate High Pressure Gas Quench (20Bar) PLUS Oil Quench |
FineCarb® – low pressure carburizing technology
Why has LPC (vacuum carburizing) achieved such success in Industry?
As a high efficiency vacuum carburizing furnace, the CMe is characterized by an extraordinarily high coefficient of carbon transfer due to the vacuum (or partial pressure) nature of the process. In the initial phase of carburizing, for example, at 950°C (1740°F), the carbon stream directed at the workpiece surface reaches the rate of 250 g/m2h. This means that, in the case of thin carburization layers, the process is considerably faster than the conventional atmosphere “gas carburizing” process.
Advantages of LPC
- Excellent carbon penetration when carburizing densely packed loads & complex shaped workpieces or blind holes parts
- Better quality thanks to no grain boundary oxidation & precise case uniformity
- Repeatable, high-speed processing
- Very low consumption of carburizing gases
- Precision via heat treating process simulation software package: SimVac (carburizing & gas quench simulator),
- Simplicity of carburizing of aircraft & alloy steels i.e.: Pyrowear® Alloy 57, M-50 NIL, SAE 9310, Ferrium® C61 alloy etc.
- Compatible with NADCAP
- High carbon potential of carburizing gas mixture (C2H2, C2H4, H2) - other gas mixtures also available
- Purity of process because of multicomponent carburizing gases mixture
- Green manufacturing process – no CO2 emission
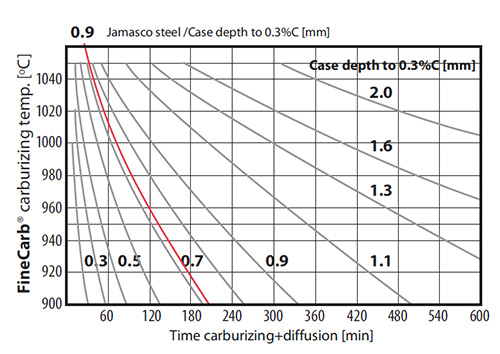 Approximate duration of vacuum carburizing process for 16MnCr5 steels, correlated to the temperature. |
SimVac™ – carburizing and quenching heat treat simulation software
This process-simulation software package enables users to design and simulate the carburizing and quenching processes (with SimCarb and SimHard, respectively), prior to running parts or trials. Optimal design and checking of process parameters will help save process time and avoid waste from scrapped parts.
Advantages
- Optimal planning for segments of the carburizing process, divided into: carburizing and diffusion stages (“boost and diffuse”)
- Calculations based on steel grade, size and shape of parts as well as cooling profile for hardening
- Automatic or manual simulation operation mode
- Simulated carbon profile comparison
- Intuitive graphical interface
- Compatible with SecoVac – furnace control system
PreNitLPC® – SECO/VACUUM's unique process enhancement for LPC!
Pre-NitLPC offers high speed and economic vacuum carburizing. Pre-nitriding for low pressure carburizing, named PreNitLPC®, allows higher carburizing temperatures and use of wider range of steel grades. PreNitLPC® is a modern, fast and economic addition to low pressure carburizing.
PreNitLPC® is a unique process offering high value in both cost of operation and process efficiency:
- Reduced carburizing cycle time
- Lower process cost
- No inter-granular oxidation
- Excellent uniformity
- Optimum carbon penetration
- No CO2 emissions
- Environmentally-friendly
For every 100 processes (i.e. for 0.6 mm effective case depth, or ECD) according to traditional carburizing methods, PreNitLPC® technology can offer users up to 40% in increased process efficiency. Optimum carbon penetration allows efficient heat treatment of complex shapes and the densely packed loads with superior case uniformity.