Super IQ®: The Next Step in Integral Quench Furnaces
Super IQ® combines the best of SECO/WARWICK’s proven hardening technologies to conduct precision carburizing -- plus higher standard temperatures -- using standard quench oils. And it integrates with your existing IQ loader designs, so no extra cost there either!
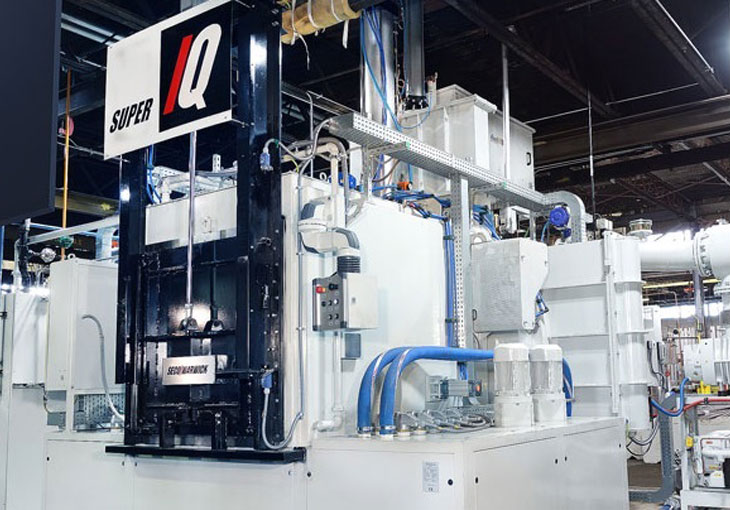
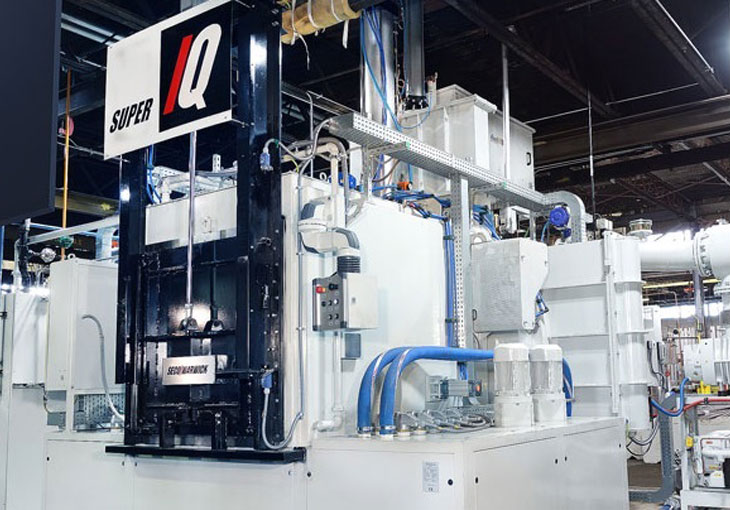
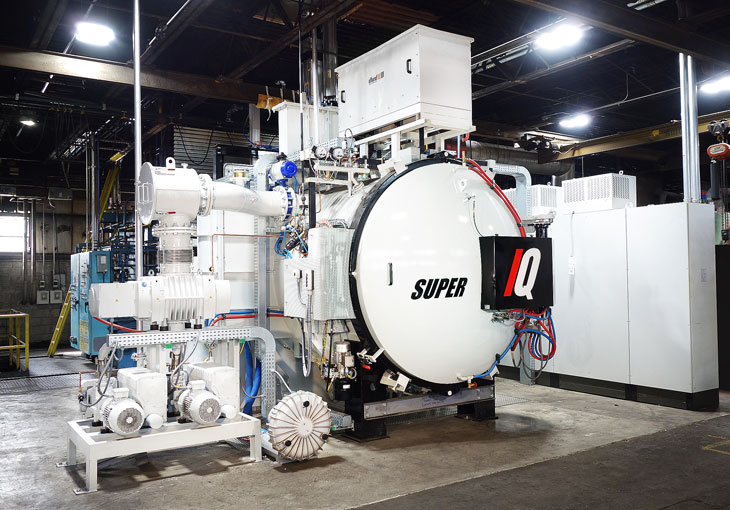
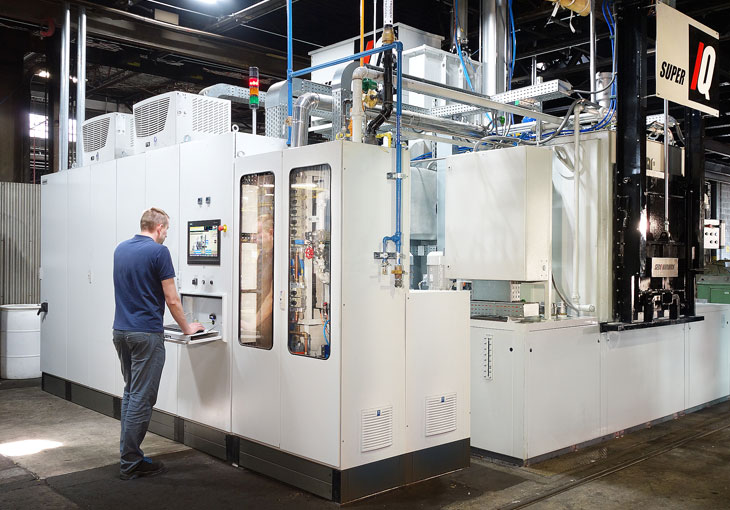
Super IQ® Does More and Costs Less
Works Better | Costs Less |
---|---|
|
|
Ask us about our Super IQ™ - Gas Carburizing!!
How Super IQ™ benefits your carburizing process
- Turn it on, turn it off. No idling or conditioning
- Clean, cool, contained thermal cycling
- Proven carburizing via low pressure carburizing
- Low use of process gases (Acetylene), Nitrogen
- Smart software via our SimCarb Software.
Furnace Benefits and Advantages
- No Endothermic Generators needed!
- High temperatures over 2000F with no damage to furnace
- Meets AMS 2750E
- Fast transport times to quench (less than 30 seconds)
- Highly agitated oil circulation design
- Fully automated processing
However, while IQ furnaces are the workhorse of heat treating for high volume processes like carburizing and through-hardening, their performance has known limitations and represent the highest maintenance item in a heat treat shop. If one tries to increase production by speeding carburizing diffusion, the higher temperatures result in exponential damage to the alloys inside the furnace, further increasing maintenance costs. Common practice is to always keep these furnaces running so as to not upset the delicate balance inside the atmosphere, which adds to operating costs over weekends or slow periods.
Atmosphere carburizing furnaces are plagued by high IGO (Intergranular Oxidation) and wide variety of case depth. Often a wider range of hardness case depths up to 0.5mm [0.020”] are used to cover process issues). Special shapes can be difficult to evenly carburize.
Finally. many aspects of the atmosphere carburizing process have troublesome environmental problems relating to waste gases, safety issues related to flames and toxic gases, ergonomics issues related to high plant heat, flame curtains, and smell, and general discomfort related to potential hazards, like idling below 1400F with high hydrogen atmosphere.
A Better Option
The proven SECO/VACUUM Super IQ furnace provides some significant upgrades on the limitations of current integral quench furnaces. The unit uses a low-pressure processing chamber together with a positive pressure inert atmosphere oil quench tank (See Image 1). The Super IQ can replace existing units and work with existing loaders and is modular so it can fit where it is needed. It can handle gross loads up to 3500 lbs. in the 36 x 36 x 48-inch workload capacity. The low-pressure furnace uses nitrogen and acetylene, so endothermic generators are not required.
More Processing Capability and Flexibility
The Super IQ receives loads in the vestibule over the quench tank for a nitrogen purge before being transferred into the heating chamber. Once sealed in the heating chamber, heating begins in nitrogen to heat the load uniformly. Low pressure levels are achieved at elevated temperatures and acetylene carburizing can begin. The stages of “Boost and Diffuse” are pre-deterimined with some of the most sophisticated software and simulators in the industry, representing decades of learning and experience. After the heating period the load is transferred to the vestibule, lowered into the quench for highly agitated cooling in standard quench oils, then raised, and offloaded.
The unit can operate at temperatures over up to 2000° F for greater processing flexibility including tool steels and performing other processes like stainless annealing, etc., all without increasing maintenance needs
The low-pressure operation of the units provides another key advantage since there is no conditioning required. The units can stop and start at any time without any quality or time penalty and a changeover to different types of loads can be accommodated at any time. This capability provides a huge flexibility boost for scheduling.
Improved Quality
The Super IQ provides better quality parts with less variation in case depth (See Image2) without issues with microstructure like intergranular oxidation (See Image 3) and decarb. This is due to the inherently better control of the gases in a low-pressure furnace and elimination of oxygen. Super IQ parts are much cleaner after heat treating. The furnace meets Class 2 AMS 2750F requirements.
Less Environmental Concern
With the Super IQ there are no open flames, no atmosphere burn-off, no CO in the plant and no high heat sources with the water-cooled walls. Endothermic generators are not needed.
Less Operating Costs
With increased productivity afforded with faster processing, especially deeper carburized cases, the Super IQ can produce more in less time, translating to a potential of $200,000 per year improvement in profit or avoidance in external processing costs (for captives). Together with the affordable initial price and no endothermic generator needed, Super IQ is an easy decision for any commercial or and captive heat-treating facility.
Image 1: The Modular Super IQ Fits into Your Current Operations
Image 2: Improved Consistency of Case Depth with the Super IQ.
Image 3: Reduced IGO Using the Super IQ.
Comparing the intergranulation oxidation on the surface of a traditional integral quench furnace (Figure a at left) with the unaltered surface of the Super IQ (Figure b at right)
Image 4: Cleaner Parts after Processing
This image shows a comparison of traditional integral quench parts appearance at left and the Super IQ at right. In the inset it shows the parts pre- and post-heat treatment.
Configuration
One size! 3,300 lbs. capacity, 36” w x 36” t x 48” deep. We kept it simple.
Conventional Oil Quench
Double chamber for batch (In & Out) work processing. Oil quench or gas top cooling.
Find out more about our Super IQ™ - Gas Carburizing!!
Furnace Features
|
Auxiliary Equipment
|
Style | SIQ-17 |
---|---|
Workload Size W x H x L | 36” x 36” x 48” (914mm x 914mm x 1219mm) |
Maximum Gross Load | 3,300lb (1500kg) |
Vacuum Furnaces
Vector®: Single Chamber, 2-25 Bar Gas Quench CaseMaster® Evolution: Multi-Chamber Vacuum Oil Quench 4D Quench Single-Piece Flow Gas Nitriding Furnace PIT-LPC™ Vacuum Carburizing Vacuum Tempering Furnace Vacuum Aluminum Brazing CVI/CVD Furnaces Super IQ®: Gas Carburizing Furnace Vacuum Furnaces for Sale
Specifications Subject to Change without Notice
