SECO/VACUUM News
A “Green” SECO/WARWICK vacuum furnace for a manufacturer of wind power plants
A recognized manufacturer of wind power plants has chosen a vertical vacuum furnace from SECO/WARWICK designed to perform low-pressure carburizing for the large structural elements (gearboxes) used in wind power plants.
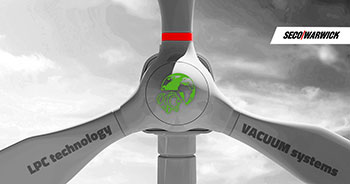
One furnace, two technologies
The solution on order combines the advantages of two technologies: atmospheric and vacuum processing. The furnace is designed for low-pressure carburizing oversized parts, made possible due to a very large, vertical heating chamber, while the furnace pit structure saves space in the production facility.
“The Pit-LPC technology is a modern alternative to atmosphere carburizing. Its main advantage is the ability to carry out efficient and effective carburizing in a much shorter time than in atmospheric furnaces. The vacuum processing solution provides more than twice the productivity, and consequently lower process costs and a quick investment return. This technology increases the safety for users, because it does not involve explosive and flammable gases. LPC eliminates direct CO₂ emissions from the carburizing atmosphere, and makes the solution ‘green,’“ said Maciej Korecki, Vice President of the SECO/WARWICK Group’s Vacuum Segment. „There is no doubt that the world is experiencing a climate crisis that requires decisive action. Renewable energy plays an important role in mitigating climate change. That is why it is important for us that we can support a partner who focuses on sustainable, renewable, and unlimited green energy,” added M. Korecki.
This is the first cooperation with this Partner in the field of vacuum technology.
Advantages of LPC technology
The main advantage of this furnace is the ability to open the furnace at process temperature at the end of the cycle. This is the advantage of atmospheric furnace technology implemented within a vacuum furnace. This type of solution combines the advantages of an atmospheric furnace with the advantages of a vacuum furnace, which include: elimination of the oxidation effect at the grain boundary, process purity, and heating uniformity. The product solves the problem of high energy and process gas consumption by the partner’s old furnaces, and shortens the carburizing process, which significantly improves efficiency and production costs.
Wind farms promise a green future
In 2021, 17 GW of wind capacity was installed in Europe, of which 11 GW were produced in European Union countries. According to a report published by WindEurope, maintaining the current pace of wind energy development will not be enough to meet the EU climate goals by 2030. Despite this, wind energy is one of the fastest growing branches of renewable energy.
The wind energy sector is under great pressure to reduce the cost of generating energy per megawatt hour. These expectations can be met by improving the turbine design to increase their operating parameters and reliability, while reducing maintenance costs.
“Wind turbine operators face the challenge of ensuring the reliability and full readiness of their equipment. Turbines experience difficult working conditions - at sea, in cold climates or in isolated places – that can adversely affect their efficiency and reliability. Therefore, it is extremely important that the parts used in their production are of the highest quality. Such quality is guaranteed by our vertical vacuum furnace. At the same time, we can reduce production costs while increasing quality. An additional advantage is the furnace’s energy savings, with this unique design provided by SECO/WARWICK,” summarized M. Korecki.
VACUUM AS AN ECO FURNACE’S ATMOSPHERE
Vacuum furnaces use vacuum (vacuum created by air evacuation) as the protective atmosphere for the heat treated part surfaces. The vacuum furnace's main advantage is their versatility and the ability to carry out processes traditionally carried out in atmospheric furnaces. Differences in the vacuum furnace construction as well as the method of conducting the processes minimizes both media consumption and emissions to the environment, making the vacuum furnace itself a SECO/ECO solution when compared to traditional atmosphere furnaces.
Vacuum heat treatment's eco-friendly features include:
/ perfect part surface quality (without additional operations)
/ no intercrystalline oxidation (no additional mechanical treatment)
/ no need to use protective gases (lower costs and emissions)
/ minimal consumption of process gases (cost savings)
/ minimum time for atmosphere preparation and conditioning (saving time and costs)
/ zero startup and shutdown time, work on demand (saving time, costs)
/ no open flame, no risk of fire or explosion (safety)
/ clean process, no part washing required (reduced environmental pollution)
/ low heat and by-product emissions (limited global warming effect)
/ environmentally friendly (zero pollution)
/ zero CO2 emissions (carbon footprint reduction)