ZeroFlow® Gas Nitriding Process
ZeroFlow® Gas Nitriding Process
SECO/WARWICK'S ZeroFlow® gas nitriding process, developed in-house, is precision nitriding using ammonia (NH3). The adjustment of the nitriding atmosphere's chemical composition, and therefore the control of nitriding potential (NP or Kn), is performed by control of NH3 feeding into the furnace. The amount of NH3 fed into the retort is adjusted and controlled with use of a gas analyzer (H2). The ZeroFlow® control process is, by definition, precision gas nitriding.
Experience has shown that the ZeroFlow® process, in conjunction with SECO/VACUUM proprietary equipment designs, is characterized by much lower consumption and emission of gases. It requires a simpler control system and allows for forming the case hardness with the same precision as in processes using double-component (blending) atmospheres.
SECO/WARWICK developed the ZeroFlow® gas nitriding process together with world-renown gas nitriding expert Professor Leszek Małdziński. Professor Małdziński is always available to advise new SECO/VACUUM gas nitriding furnace users.
Advantages of Gas Nitriding using the ZeroFlow® Process
- Lower ammonia consumption
- Simplified gas system
- Optional – ferritic nitrocarburizing (FNC) with or without post oxidation (black)
- High accuracy of forming the nitrided layer due to precise control and gas equilibrium characteristic of the process
- The gas nitriding process is fully controlled by only ammonia additions, along with occasional flow stops – ZeroFlow®
- Low consumption of nitrogen due to vacuum purging of the retort
- Quick and precise atmosphere analysis in-situ in the closed system, no external gas sampling installations required
- Investment costs are lower
- Operating costs are lower
- ZeroFlow® is gas nitriding of steel
Examples of parts nitrided with use of ZeroFlow® process
Nitriding of plates for casting glass bulbs for lamps ![]() |
Nitriding of inlet sleeves with the pushing piston, used in molds for aluminium pressure die casting ![]() |
Nitriding of crankshafts for engines of racing cars ![]() |
Nitriding of toothed wheels for wind power plants ![]() |
Nitrocarburizing and post-nitrocarburizing oxidation of shafts ![]() |
Nitrocarburizing of piston rods in the automotive industry ![]() |
![]() |
![]() |
Control system properties
- Fully automatic machine operation
- Unlimited number of recipes, created by the process engineer
- All process historical data, presented as diagrams on the screen, may be stored on the hard drive
- Possibility of exporting the historical and alarm data out of the system for further analysis (e.g. to .csv files)
- Logging of the most important historical data in files and/or any data base of the customer
- UPS system and power failure scheme assuring safety of operation and production
- Possibility of re-starting the process after power interruption
- Specialized software allows for remote monitoring and control of the furnace operation
- Work time counters for planning preventative maintenance.
- Optional balancing of media: gases / water / energy / heat (range: total, process, user) with the supply source level control (tank level + alarms, tank filling)
- A wide offering of SECO/WARWICK solutions for gas nitriding includes modern tools that assist process/recipe design
- A simulator of nitrided layer growth by alloy grade enables off-line programming and verification of recipes (optional)
- Setting basic values of nitriding furnace control parameters, namely temperature, nitriding potential, as well as segment times, enables precise nitriding case control.
Frequently asked questions
Does nitriding with the use of ZeroFlow control obtain the same results as other nitriding methods?
Definitely yes. It is the gas nitriding process, based on continuous adjustment of the nitriding potential. It can create the same precision nitrided cases as the FLOE method and also as with Ion (Plasma) nitriding.
Does use of ZeroFlow® process allow for gas nitriding without creating the white layer of nitrides?
Definitely yes. Proper adjustment of the nitriding potential allows for nitriding without creating the white layer. ZeroFlow control is actually a more precise process than many other nitriding potential control methods. For more in-depth questions, contact the SECO/VACUUM gas nitriding experts.
SECO/VACUUM Furnaces for gas nitriding
Two basic types of furnaces are used which have been perfected for over 20 years! - horizontal retort – type HRN, and vertical retort (pit) – type VRN. Various standard sizes and custom sizes are offered.
SECO/VACUUM Furnaces for ferritic nitrocarburizing (FNC)
The same gas nitriding furnace designs are used for ferritic nitrocarburizing. The option of CO2 (carbon dioxide) or other carbon gas, i.e. CO, is added automatically. Carbon potential control (Kc) is also an option. Post oxidation (black color) is also an option.
SECO/VACUUM Nitriding Furnaces for aerospace (NADCAP and AMS)
Aerospace specifications often require the furnaces to meet AMS 2759 parameters and the processes contained in various specifications require the use of a small ammonia dissociator to assist with nitriding potential control, which SECO/VACUUM supplies, as an option. The furnace designs are the same SECO/VACUUM gas nitriding furnaces as for vertical and horizontal applications. Contact your SECO/VACUUM representative for further details.
Recap of SECO/VACUUM gas nitriding furnace features:
- Special door sealing system
- Vacuum system for removing air (reduces nitrogen consumption) and purging nitriding atmosphere from the retort
- Simple adjustment of gas nitriding potential via the ZeroFlow® control process by measuring the hydrogen content (% H ) in the atmosphere, and by adding ammonia, as needed
- System of accelerated atmosphere gases cooling after nitriding (Turbo cooling option)
- Low nitrogen consumption, which is used only for the auxiliary operations: safety purge and maintaining overpressure during cooling
- Simple system of neutralizing exhaust gases from the furnace, consisting of a small exhaust gas burner system
ZEROFLOW is GAS NITRIDING!
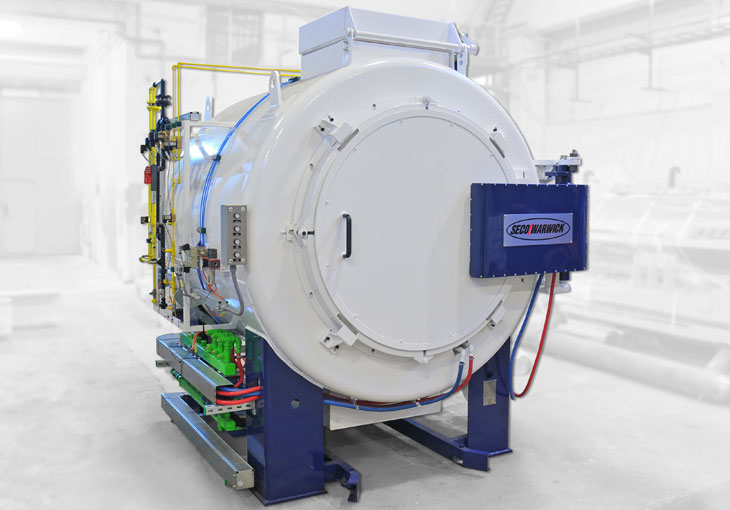
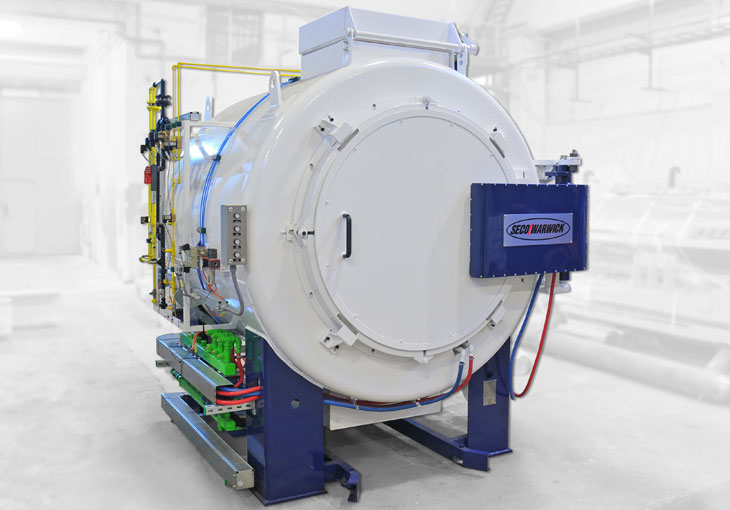
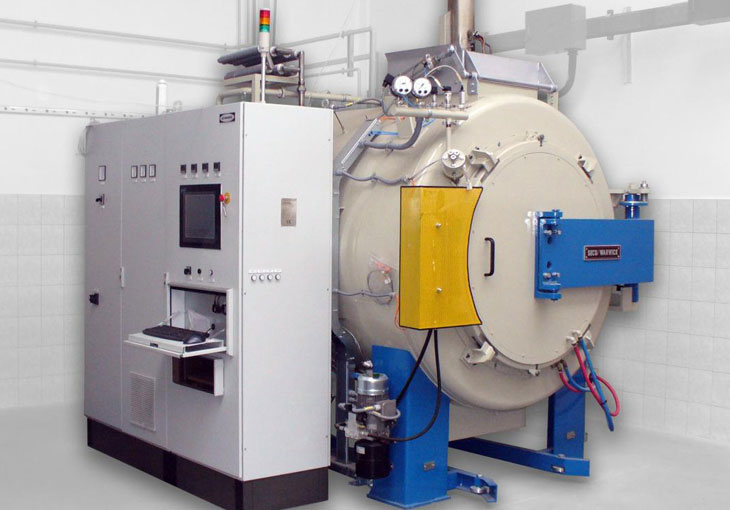
Vacuum Furnace Processes
Fine Carb®: Vacuum Carburizing High Pressure Gas Quench High Vacuum Furnaces PreNit: High Speed Vacuum Carburizing Vacuum Brazing: Advanced Front Loading Gas Nitriding with ZeroFLow® FURNACE/PLUS Vacuum Circuit Breaker Brazing
Specifications Subject to Change without Notice
